USW Local Union 13-750, Shell work together to safely execute ram pump job
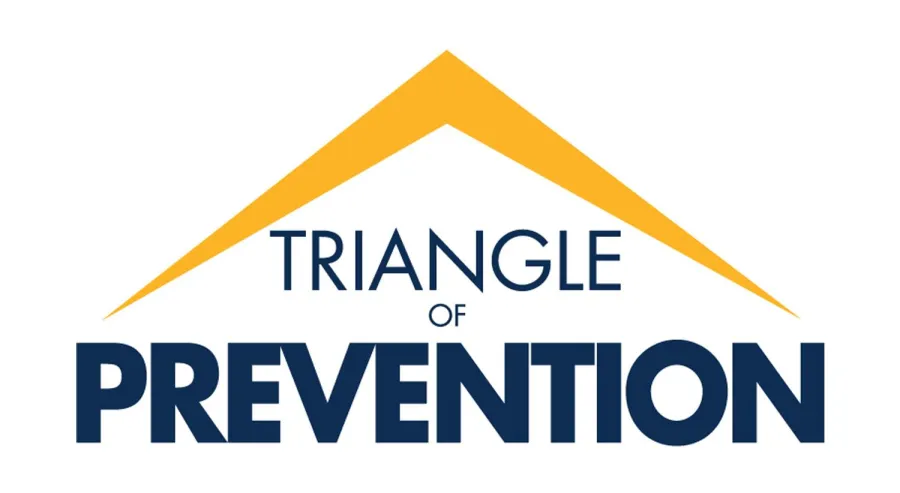
In the fall of 2019, Operations, Maintenance, Safety and the United Steelworkers (USW) Local Union 13-750 worked together to safely execute a ram pump job on the H-Oil unit.
What is a ram pump job?
A ram pump is a manually-operated hydraulic pump which uses diesel-type material to assist in unplugging piping, tubing or other connections plugged from process operations. The ram pump equipment hooks up to process equipment through a threaded connection to use hydraulic pressure to free up plugged equipment. The ram pump equipment pumps small amounts of fluid into the plugged piping/tubing which pressures up the line and attempts to clear obstruction from the process equipment. Ram pumping is periodically done on H-Oil, as H-Oil is a heavy oil conversion unit.
The task to be performed consisted of using the ram pump equipment to unplug an instrument tap located at the top deck of the Train 200H-Oil Reactor. This instrument tap supplies a reading to a transmitter which reads a differential pressure across a grid bed in the reactor. This pressure differential transmitter is a key monitoring point to assist with forecasting the safe operation of the Reactor. This instrument tap and tubing runs from the top to the bottom of the reactor and operates at a high pressure and temperature. The task of ram pumping at the top of the Reactor presents many hazards to be addressed prior to beginning permitted work. During pre-job walks conducted by the field operators and maintenance crafts, they identified high temperature, high pressure, zero energy and egress routes as hazards associated with the task. These hazards raised concerns with the field operators and maintenance crafts during the job site walk visit. Operations, Maintenance and the safety representatives from Local 13-750, which include members of the Triangle of Prevention (TOP), Process Safety Management (PSM) and Joint Health and Safety Committee (JHSC) initiatives, escalated the concerns observed by the team in the field to H-Oil supervision. During the conversation between Local 13-750 safety representatives and H-Oil supervision, it was agreed to perform a formal Job Safety Analysis (JSA) to help with identifying the hazards for each job step to ensure a proper mitigation was in place for each identified hazard.
A formal JSA requires everyone involved in a job to be involved in writing the formal JSA, including operators, safety representatives, craftsmen, maintenance supervisors and staff support. This includes the operator writing and issuing the permit, and the craftsperson performing the work. Once everyone is present in the meeting, the group breaks down the job step by step, where hazards are recognized and identified for each step. Once a hazard has been identified at a step, the group does not move on to the next step until that hazard has a mitigation assigned to it. Even the seemingly insignificant first step, such as removing a plug or cap on a bleeder to install the ram pump, is discussed by the group, hazards are recognized, and mitigation is assigned to those hazards. The JSA took about two and a half hours to discuss, document and agree upon. All hazards were identified and mitigated. The production supervisor facilitated the meeting and documented the JSA. This formal JSA involved Pressure Equipment Integrity (PEI) for integrity concerns and unit engineers for process support. Once the JSA was complete with everyone’s concerns being discussed and addressed, Operations and Maintenance conducted the job site visit and executed the work following the guidelines of the formal JSA. The ram pump job was safely and successfully completed without an incident.
This was an excellent example of collaborating for the best possible outcome regarding personal and process safety. Local 13-750, through the representatives within TOP, PSM and JHSC, and hourly-represented employees, worked together with Shell staff and contractors to resolve any safety issues that needed to be addressed, and followed proper procedures prior to a job being performed. Hazard recognition and stop-work process were also notably used. This event was also recognized during the “Grade the Week” presentation at the Site Alignment meeting. The “Convent’s Ways of Working” section of “Grade the Week” recognized the H-Oil JSA collaboration across the Local, staff and contractors as an example of Collaborating for Best Decisions and Outcomes.
“The TOP and USW safety representative positions are not only valuable to keeping our USW brothers and sisters safe, and bringing concerns and underlying issues up to management,” TOP Representative Matt Bourgeois of Local 13-750 said, “these positions also provide safety council for contractors.”
“It has been stated in numerous conversations by our core contractors: thanks for taking the time to listen and address our concerns and keeping us safe.”
“The idea that has been for years, is that contractors do what they are asked to do and not to ask questions. That idea needs to change and we plan to keep working on this change.”
“These positions make bringing safety issues and concerns forward easier for a lot of people,” Bourgeois said. “Maybe employees don’t feel comfortable bringing their concerns to company safety members, or they feel like nothing will happen if they do because it was brought up many times. So that’s where we step in, we have built relationships with the employees in the field over many years. Employees trust and feel comfortable talking to us. At the end of the day we all, contractors and company employees (USW members), need to safely return home to our loved ones.”
Image courtesy of theadvocate.com.